Bioplastics: Japanese SMEs Leading Advancements in the Industry
Japan’s bioplastics industry is advancing as smaller companies find creative ways to upcycle biomass waste, like making helmets from leftover scallop shells.
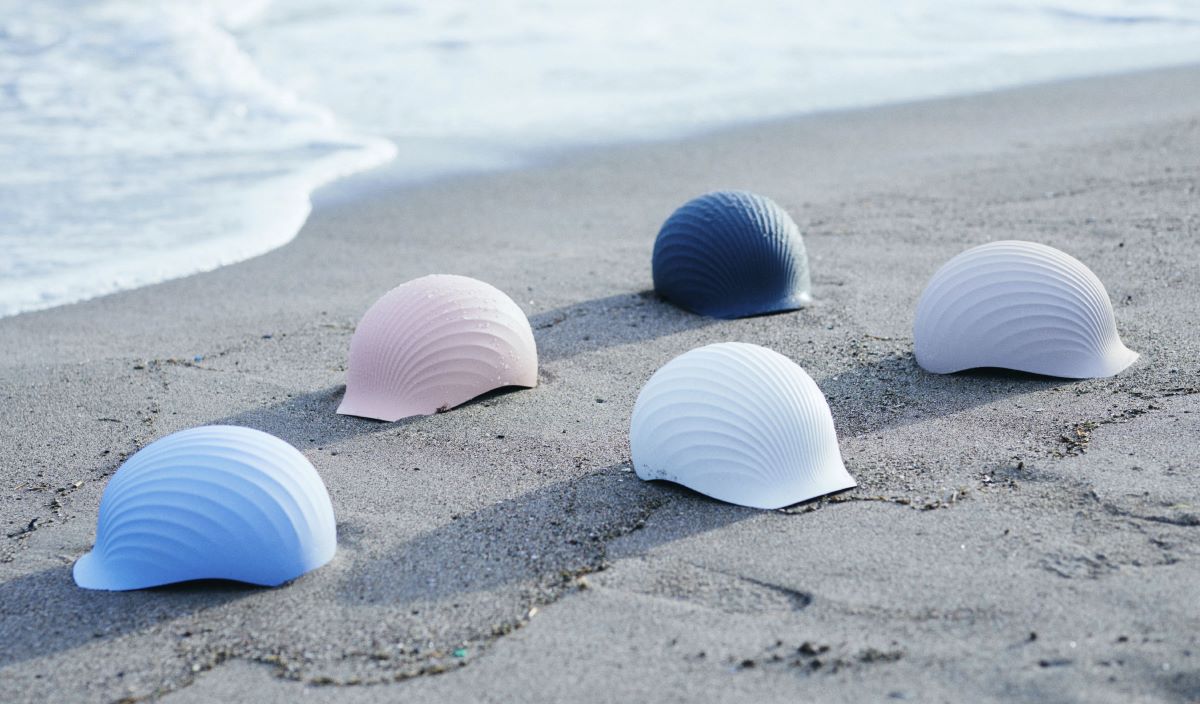
このページを 日本語 で読む
Small and medium-sized venture companies are increasing their presence in the field of biomass plastics, or bioplastics, which produce less carbon dioxide than conventional plastics made from petroleum.
Using proprietary technologies, these companies are producing bioplastics from a range of biomass resources. These include rice unsuitable for human consumption, seashells, and wood waste. Some have even launched finished products made from bioplastics.
Scallop Shells Become Bioplastics
One such company, Osaka-based Koushi Chemical Industry, developed its "Shellstic" bioplastic using scallop shells as raw material. Researchers at Koushi Chemical opted to use these shells, which have calcium carbonate as their main component. The shells are ground into a powder and then mixed with waste plastic. The resulting hybrid plastic can reduce CO2 emissions by up to 36% compared to newly-produced petroleum-based plastics.
Staff at Koushi Chemical came up with the idea of upcycling scallop shells when they learned of a scallop-producing region that was having trouble disposing of leftover shells after scallop processing. The shells are provided by Sarufutsu Village in the far north of Hokkaido, one of the most well-known scallop-producing areas in Japan.
Koushi Chemical also developed the "Shellmet," a helmet made from Shellstic. Preorders for the helmets on the Makuake crowdfunding site far exceeded the company's targets. The company aims to begin filling orders for the helmets in May, and then launch general sales in June.
Rice as Biomass
Tokyo-based Biomass Resin Holdings is expanding production of its "RiceResin" bioplastic made from rice not suitable for consumption. The firm constructed its third factory in December of 2022 in the town of Namie in Fukushima Prefecture.
The company is growing rice in paddies in Namie that had been left fallow after the 2011 nuclear accident. Its other factories are located in Minamiuonuma City in Niigata Prefecture and Minamata City in Kumamoto Prefecture.
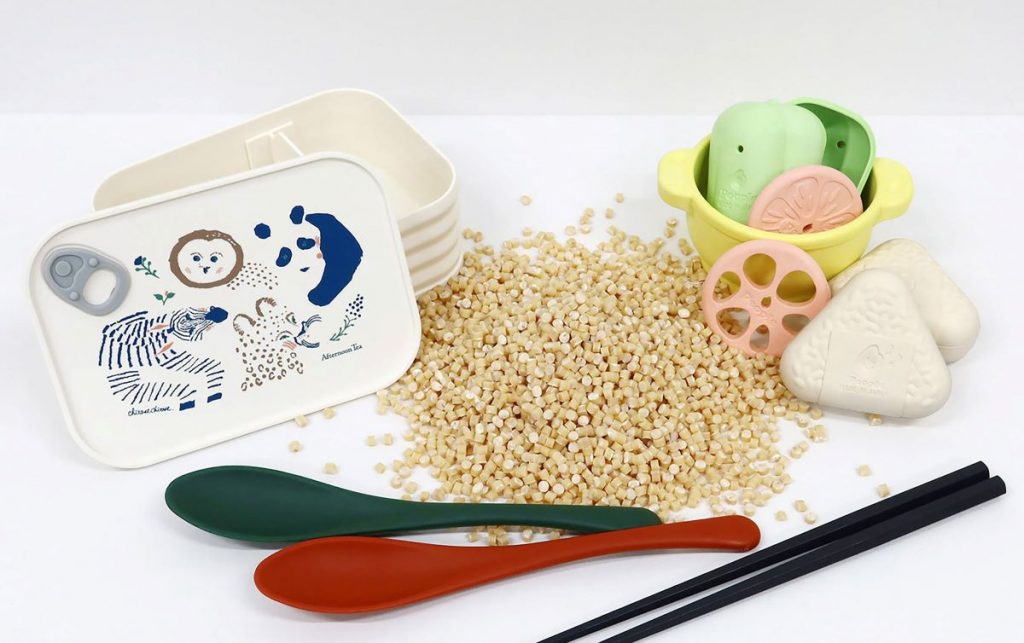
RiceResin mixes rice with the raw materials for conventional petroleum-based plastic at ratios of up to 70% rice. CO2 emissions are decreased by the amount of rice used.
The company is expanding uses of its bioplastic to include items such as spoons, toys, and garbage bags.
Business Innovation Partners, a company based in Kawasaki, has also developed a bioplastic. Named "HEMIX," the bioplastic uses a previously difficult-to-extract component found in wood waste.
HEMIX is made from hemicellulose, a component that makes up 20-30% of plants and trees. It is difficult to extract and process, and so was commonly burned or thrown away.
But then the company discovered the perfect conditions for extraction. HEMIX can also be made biodegradable, as microbial activity ultimately breaks it down into CO2 and water.
Bioplastics for Differing Uses
Heiwa Kagaku Industry, a company based in Ichikawa City, Chiba Prefecture, is taking a slightly different approach. It owns technology enabling it to layer multiple plastics with different properties to create products such as bottles and other containers for foods and cosmetics.
An increasing number of companies, especially large firms, are using bioplastics in containers for their products. However, as Harumasa Hatakeyama, Managing Director at Heiwa Kagaku, explains, "there is no universal material that can be used in any situation."
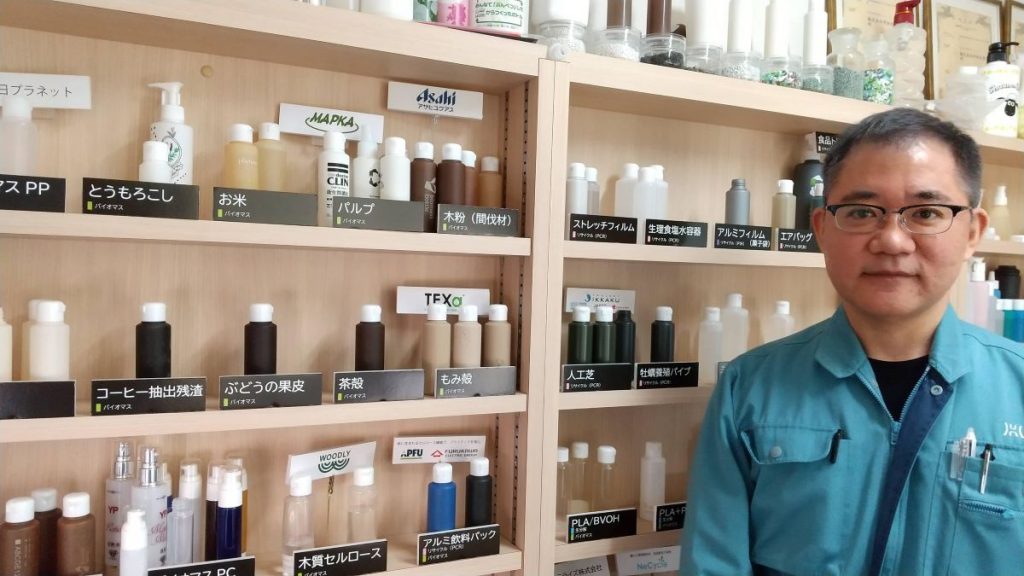
Bioplastics, for example, allow water to permeate and therefore can’t be used as the sole ingredient in containers that store liquids. They must be layered together with impermeable materials such as petroleum-based plastics.
Heiwa Kagaku can create bottles made of up six materials arranged in nine layers (including adhesives), allowing for various uses of bioplastics according to needs.
The Resource Circulation Strategy for Plastics compiled by the government in May 2019 calls for Japan to introduce two million tons of bioplastics by 2030.
Ichiro Fujita, Group Leader at the Japan Finance Corporation's Research Institute, maintains that when it comes to technologies, small and medium-sized companies are "holding their own".
"They can handle production in small lots, something that big companies don’t do. This leads to breakthroughs in bioplastics," Fujita adds.
このページを 日本語 で読む