Can Waterless Digital Textile Printing Clean Up the Fashion Industry?
Digital textile printing that uses a minimal amount of water and reduces waste could mend the reputation of the world's second most polluted industry – fashion.
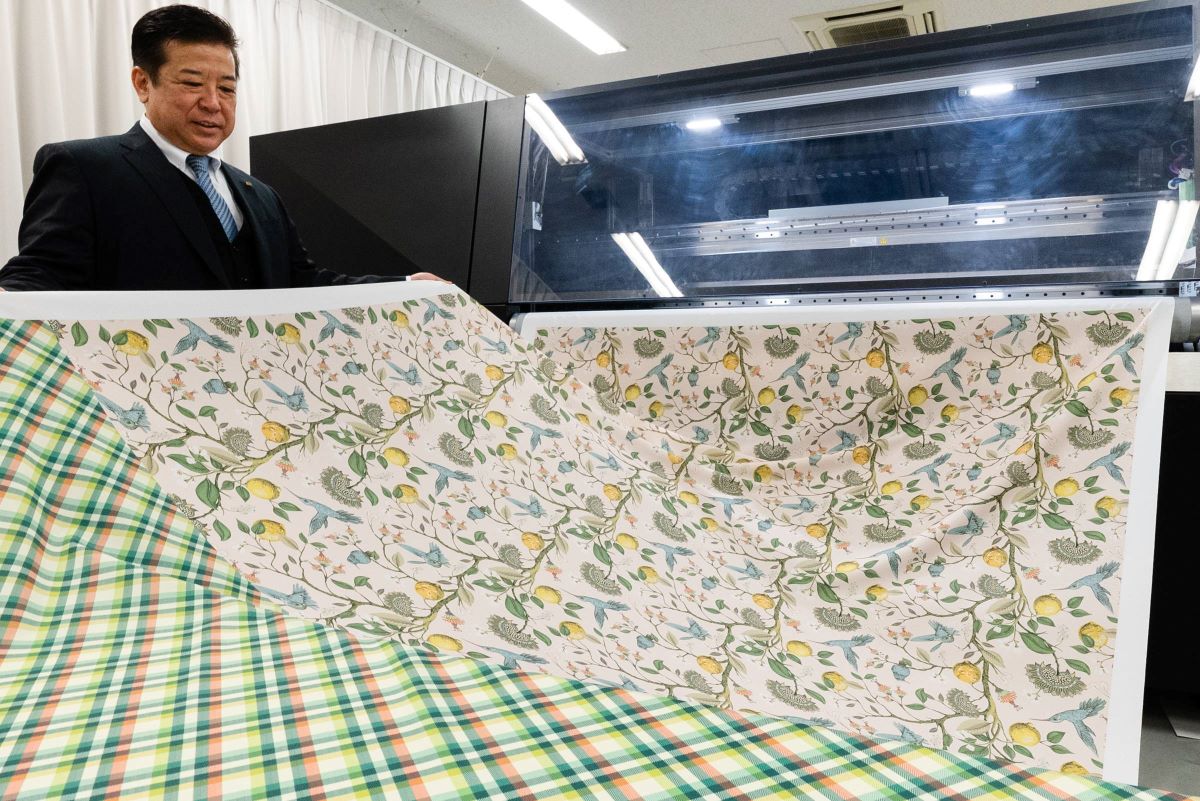
このページを 日本語 で読む
The emergence of digital textile printing, a technology utilizing inkjet printers to apply patterns to fabric, is gaining popularity in the apparel sector. The fashion industry, often criticized as the world's second most polluting industry, faces substantial challenges in excessive water consumption and massive product waste.
Digital textile printing presents a potential solution. It has made remarkable strides in reducing water usage to less than 1% that of conventional methods. Additionally, it holds the promise of curbing waste through small-batch production. This eco-friendly approach is gaining recognition for its pivotal role in addressing environmental concerns within the industry.
20% of Wastewater Globally
Clothing is an indispensable part of daily life, but the industry has recently come under scrutiny for its considerable environmental impact. According to the United Nations Conference on Trade and Development (UNCTAD), the fashion industry consumes approximately 93 billion cubic meters of water annually. About 20% of industrial wastewater globally stems from dyeing and processing textiles.
Crafting just one pair of jeans demands 7,500 liters of water – equivalent to a seven-year drinking supply for one person. However, it is not just water consumption that is problematic in clothing manufacturing. The widespread adoption of low-priced fast fashion has accelerated the cycle of mass production and consumption.
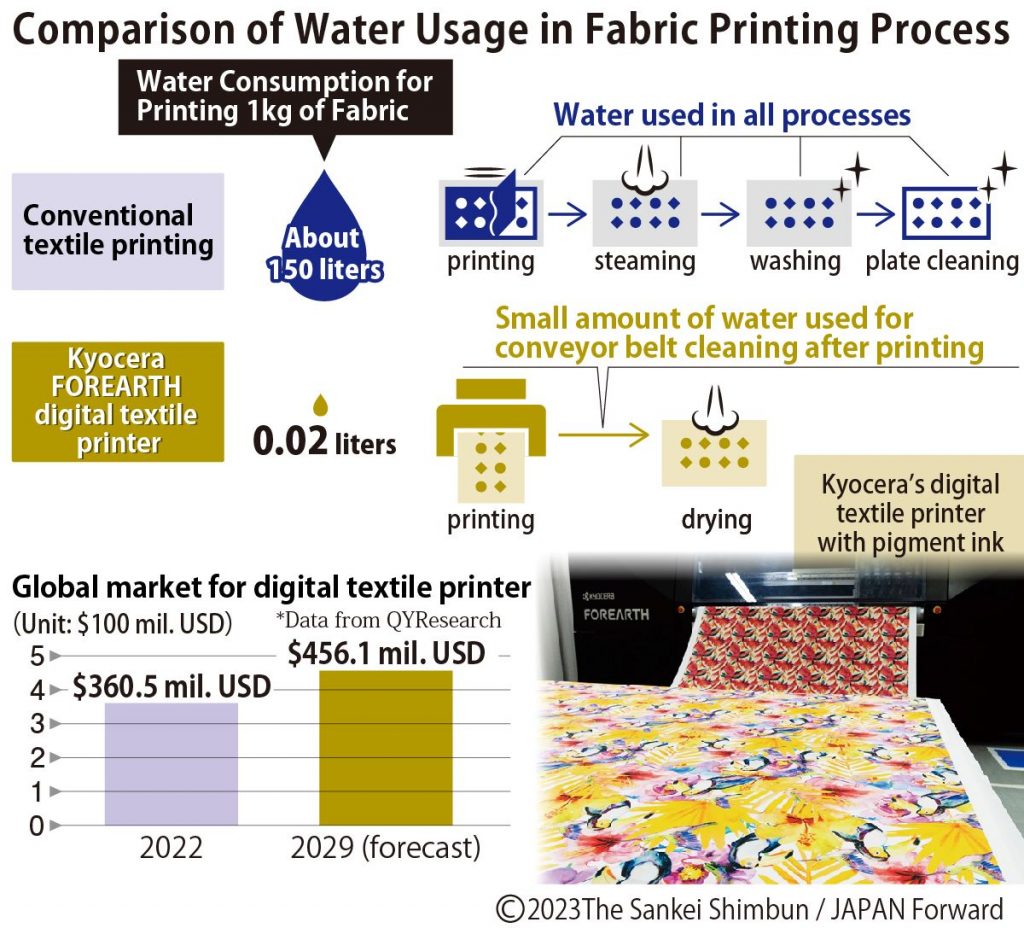
Drawing attention in this context is digital textile printing. As the name implies, it is a technique that prints designs on fabric based on digital data. Similar to printers for paper, digital printing on fabric applies ink from an inkjet head, eliminating the conventional step of creating printing plates.
In the past, the cost of producing printing plates required large-scale production to bring down the cost per garment. However, digital textile printing requires no printing plates, making small-batch production viable. Manufacturing only the needed quantity allows for the potential to reduce unnecessary waste.
Water consumption: 0.02 Liters
The type of ink used in digital textile printing significantly influences water consumption. Pigment ink uses almost no water but has limited applications. Meanwhile, dye ink consumes a certain amount of water but accommodates any kind of fabric. Both options are known to have pros and cons, yet Japanese companies are challenging these accepted conventions through ongoing research and innovation.
Kyocera recently unveiled FOREARTH, a digital textile printer for pigment ink that uses almost no water. Along with extremely low water consumption, pigment ink enables intricate printing and ensures excellent lightfastness. In the past, pigment dye was only used for limited items like T-shirts due to making the printed area of the fabric stiff.
Kyocera has overcome this limitation with its proprietary pigment ink that incorporates special pre- and post-processing solutions. The result is a soft finish comparable to dye ink. The printer is versatile enough for printing on various fabrics, including natural fibers like cotton and silk, as well as polyester and other synthetic fibers. This breakthrough has not only enhanced printing quality, but also bolstered overall production efficiency.
Added Benefits
The biggest change brought about by the adoption of pigment ink across a range of clothing is in water usage. Conventional fabric printing involves massive water consumption for processes like printing patterns, steaming to set colors, and washing to remove excess dye.
Printing on one kilogram of fabric typically uses around 150 liters of water. However, with the FOREARTH using pigment ink, this amount is remarkably reduced to just 0.02 liters. While minimal water is employed to wash away lint and debris adhering to the conveyor belt that moves the fabric, the need for water in the printing process is basically eliminated.
This reduction in water usage also eliminates constraints textile printers can be installed. The need to put factories along rivers for wastewater discharge is eliminated. And the absence of washing processes allows for significantly shorter production lines, reducing line length from about 100 meters to just 10 meters. These machines can now be installed in urban areas where apparel manufacturers are concentrated. Transport distances are also minimized, contributing to decarbonization efforts.
Sho Taniguchi, Deputy General Manager of Kyocera's IDP Business Development Division, explains. "Initially, many customers were hesitant to work with pigment ink. But once they witness the actual print quality, they are more and more willing to use it," he said.
Environmental Considerations First
The Seiko Epson Corporation, a pioneer in digital textile printers for the last two decades, presents a diverse product lineup accommodating both pigment and dye inks. But according to the company, approximately 90% of producers in the fashion industry still adhere to conventional methods despite significant strides in digital textile printing.
While dye ink products have historically dominated the digital textile printing landscape, Kazuomi Okuzono, General Manager of Seiko Epson's C&I Printer Sales Division, has observed a notable shift. "Over the past 2-3 years, orders for pigment ink-compatible products have surged. Currently, orders are nearly on par with dye ink."
Although dye ink does reduce water consumption by about half for digital textile printing, the remarkable water-saving potential of pigment ink is making it the preferred choice for many companies.
This trend is underpinned by heightened global environmental consciousness and stricter regulations on industrial wastewater and clothing disposal, particularly in Europe. The fashion industry is faced with the urgency of adopting digital textile printing. Major brands are asking for fabrics produced using pigment ink digital textile printers, putting environmental considerations first.
However, the complete transition of all subcontracting factories to digital textile printing is problematic. Some products are still unsuited for pigment ink use. Okuzono emphasizes, "An industry-wide shift won’t happen until digital textile printing accounts for 30-40% of the total. We aim to contribute by offering a diverse lineup with a range of prices and ink types."
"International luxury brands meticulously scrutinize details like wastewater disposal methods when contracting with dyeing factories," cautions Associate Professor Hiroko Takeshita of Ehime University's Faculty of Education. "Failing to address environmental impacts may lead to a loss of customers," she adds.
このページを 日本語 で読む