World's Strongest and Most Eco-Friendly Magnets Win Honda Prize
Inventors of industry-revolutionizing neodymium magnets were recently awarded the Honda Prize for their contribution to advancing environmental technology.
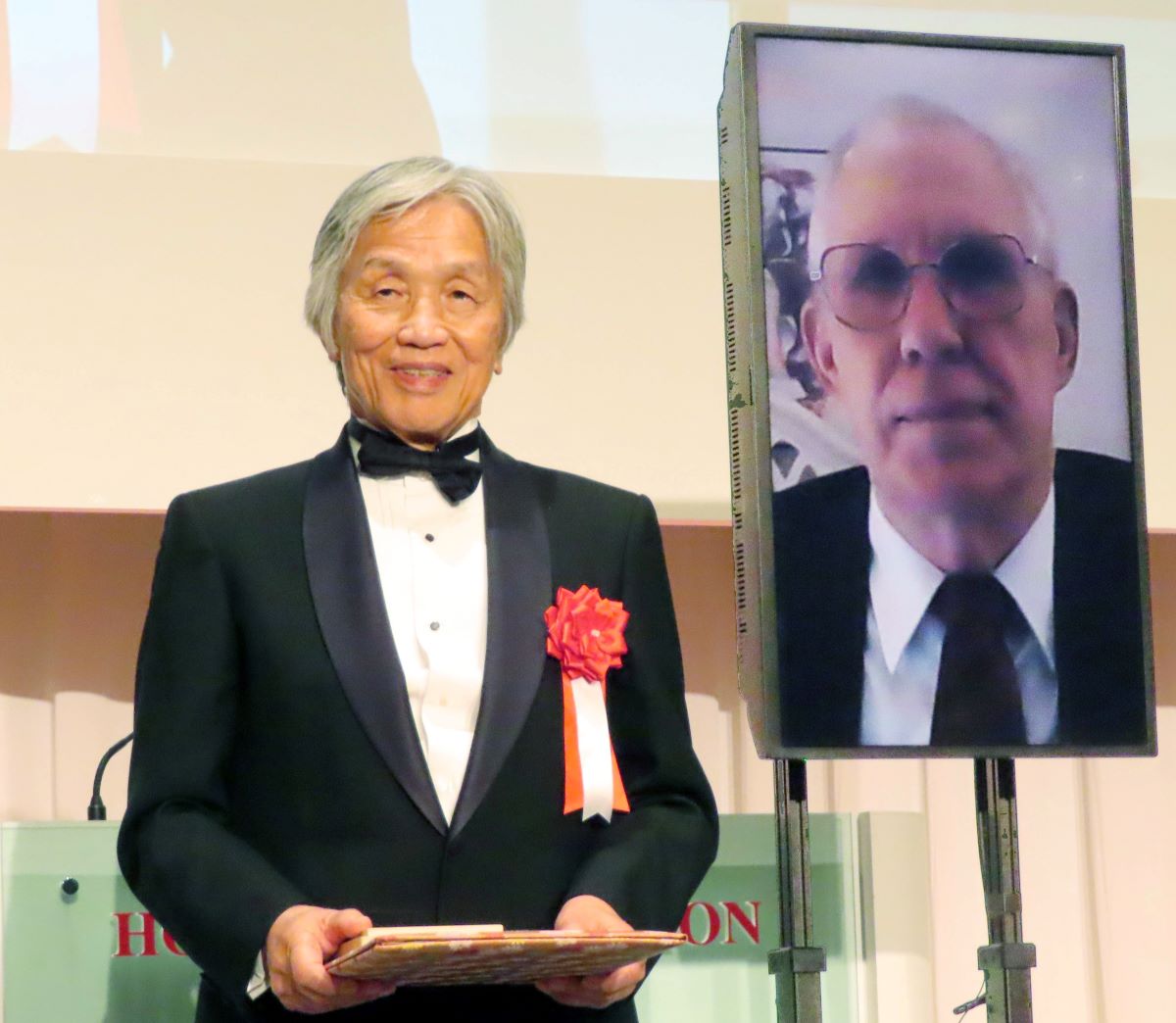
このページを 日本語 で読む
The Honda Prize is an international award that honors contributions to ecotechnology. In 2023, the Honda Foundation awarded the prize to the inventors of neodymium magnets, Dr Masato Sagawa and Dr John Croat. As the world's strongest permanent magnet, it paved the way for the practical application of high-performance motors. It also revolutionized society by making electronic devices smaller and more energy-efficient.
Sagawa is an advisor to Daido Steel, and Croat is a former managing director at US-based General Motors (GM). In 1982, they independently developed different neodymium magnets using entirely different manufacturing methods. There has also been talk of the neodymium magnet being a Nobel Prize contender. So, just what are these magnets?
The Magnet that Transformed Society
A neodymium magnet is a permanent magnet composed mainly of the rare earth elements neodymium, iron, and boron. Adding a small amount of dysprosium, another rare earth element, to the magnet generates the world’s strongest magnetic force. A neodymium magnet weighing only one gram is strong enough to attract and lift three kilograms of steel. It is dozens of times stronger than ferrite magnets, the most common black-colored magnets widely used in stationery and household goods.
Neodymium magnets help reduce the size, weight, and power consumption of various motorized equipment. They have become indispensable for the latest industrial products. They are used in electronics like hard disks, phone vibrators, and air conditioners. In addition, neodymium magnet applications are expanding to wind power generators and hybrid and electric vehicles.
One unusual application is in motors used to hoist elevator cables. They have eliminated the need for elevator machinery rooms typically located on the rooftops of buildings and apartment blocks. More efficient use of buildings is now possible even in Japan, where land space is limited.
Combating Global Warming
Reports suggest that motors consume 40-50% of the world's electricity. In Japan, with its advancing high-tech technology, the number is reportedly more than half. Using neodymium magnets in all motors will save a considerable amount of electricity. This is directly linked to mitigation of global warming through the reduction of greenhouse gas emissions. Therefore, demand for these magnets is only increasing.
Global Information, Inc. (GII), a market research firm, issued a report in 2023 on the current global market for neodymium magnets. The report estimates that the market is worth about $1.8 billion USD (approximately ¥265 billion JPY). Furthermore, the report projects the market to reach approximately $3.2 billion USD (about ¥470 billion JPY) by 2030.
Honda Motor founder Soichiro Honda established the Honda Foundation, currently headed up by Hiroto Ishida, President, to promote ecotechnology. Highly impressed by magnet's invention, the foundation selected Sagawa and Croat as this year's Honda Prize laureates. An awards ceremony was held in Tokyo in November. The winners received commemorative medals and a total of ¥10 million JPY (approximately $70,000 USD) in prize money.
An 'Impossible' Combination
Until the 1970s, the samarium-cobalt magnet was the world's strongest permanent magnet used in many industrial products. These magnets combine the rare earth element samarium with the metal cobalt. However, as both were scarce and costly resources, cheaper and more powerful magnets had to be developed. During their research and development, Sagawa and Croat worked at Sumitomo Special Metals (now Proterial) and GM, respectively.
By coincidence, both men came up with the same idea of using inexpensive iron and neodymium as magnetic materials. Neodymium is also a rare earth but is more abundant than samarium. Many in the science community believed these materials could not be combined in a magnet. Nevertheless, by adding trace amounts of boron to elicit a magnetic force, both succeeded in developing neodymium magnets in 1982. Initially, the magnet's heat resistance was low. But by adding the rare earth element dysprosium, the heat resistance improved to withstand temperatures up to 200 degrees Celsius. This improvement enhanced its utility.
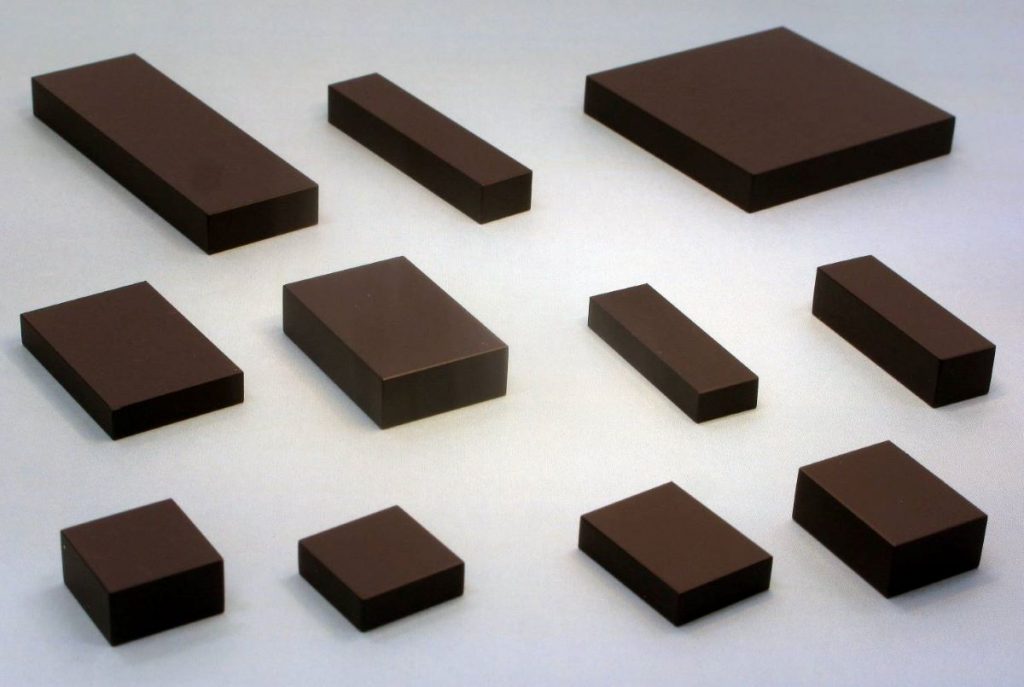
Although Sagawa and Croat used the same raw materials in their neodymium magnets, they differed in their manufacturing methods. Sagawa produced his magnet through sintering. In the sintering process, raw materials are melted to make ingots. These ingots are then crushed into a powder, placed in a mold, and baked to harden.
Large pieces of the fired product are cut into desired sizes and marketed as sintered neodymium magnets. For this reason, their main application is in relatively large motors. Early magnets were tough, brittle, and prone to rusting, but recent years have seen improvements.
'Still a Work in Progress'
Croat, on the other hand, used the rapid solidification process. In this method, melted raw materials are cast onto a cooled spinning drum. When the molten material contacts the cold surface of the drum, it rapidly solidifies. The material is then ground into a thin amorphous ribbon, mixed with plastic, rubber, or other binding material, and hardened. These magnets are known as bonded neodymium magnets.
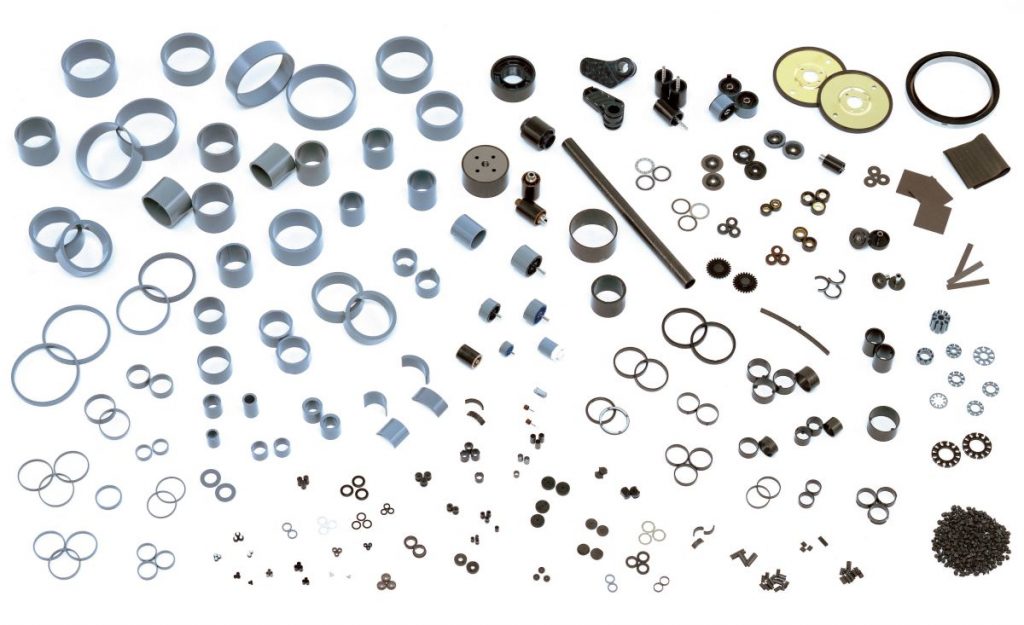
Though less magnetic than sintered magnets, they are easier to manufacture and mass-produce. Soft and pliable, the material can be molded into various shapes, including rings and thin, fine magnets. They are primarily used for precision machinery, such as computer peripherals.
Although now retired from the forefront of research, Croat recently sat down for an interview with The Sankei Shimbun. "It is deeply moving to see how my magnet has revolutionized the world," he said. "Bonded neodymium magnets have already reached a state of perfection. I believe they will continue to serve society well into the future," he added.
Meanwhile, Sagawa continues his research on enhancing the performance of sintered neodymium magnets. In response to the recent shift away from rare earths, he has successfully developed neodymium magnets that do not require dysprosium. China produces most of the world's dysprosium, raising concerns about stable supplies of the rare earth element.
Currently, Sagawa is developing a new method to refine the production of sintered neodymium magnets. Instead of producing ingots and cutting them into pieces, he aims to create sintered magnets cut to the desired size from the start.
Sagawa comments, "Neodymium sintered magnets are still a work in progress." He also expressed his hope to "continue to contribute to society by further improving their quality."
このページを 日本語 で読む