Nippon Steel Advances Hydrogen Technology to Cut CO2 Emissions
If Nippon Steel can successfully develop the technology use hydrogen in place of convention coal in steelmaking, it could cut CO2 emissions by up to 50%.
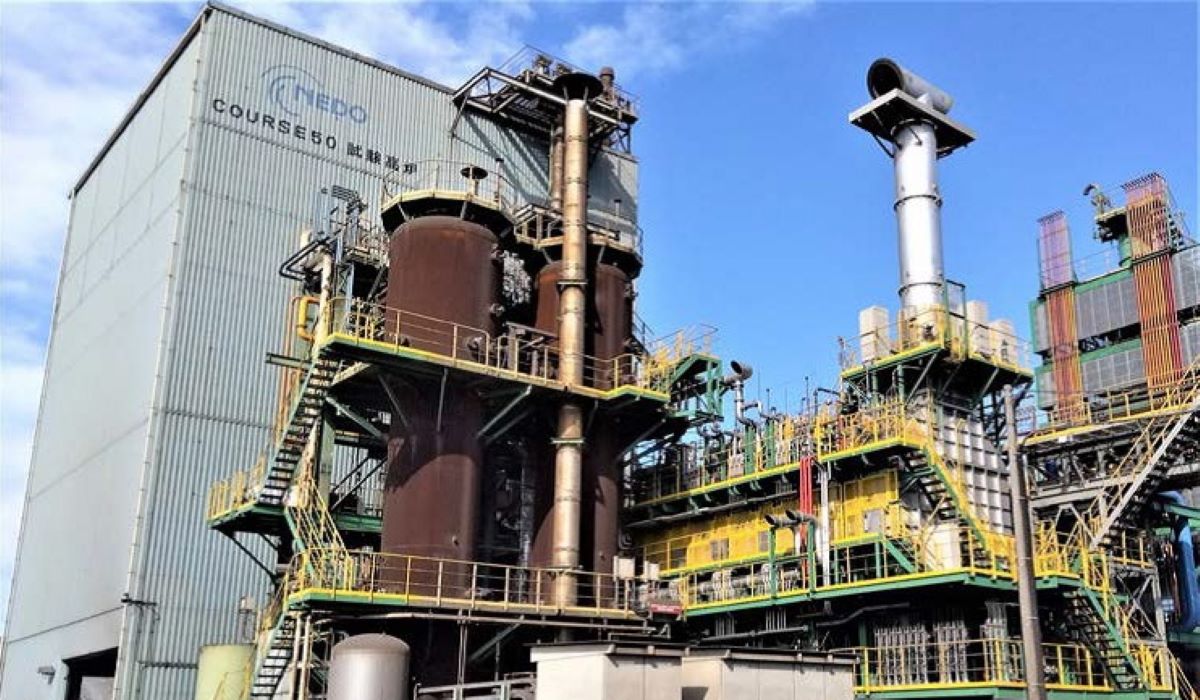
このページを 日本語 で読む
Nippon Steel is moving toward a next-generation steelmaking technology that significantly reduces carbon dioxide (CO2) emissions. Conventionally, steel is produced from iron oxides extracted from iron ore, the raw material. Oxygen is removed through a chemical reaction (reduction) with coal (carbon), resulting in CO2 emissions. This involves about two tons of CO2 emissions per ton of steel produced.
In the next-generation technology, hydrogen plays the role of coal. At its test facility, Nippon Steel has achieved 33% less emissions, the world's highest emissions reduction for steelmaking.
Temperature Control Is Key
The technology being developed is called hydrogen reduction for blast furnaces. It is part of a research project promoted by the New Energy and Industrial Technology Development Organization (NEDO) using the government's Green Innovation Fund. Nippon Steel is taking the lead on the initiative.
Blast furnaces produce steel on a large scale using iron ore as raw material. High temperatures can reach up to 1,500 degrees Celsius. Reduction using coal can be continuously performed alongside iron melting due to the exothermic reaction of heat generation that releases heat.
On the other hand, hydrogen reduction is an endothermic reaction that absorbs heat. This causes the temperature in the blast furnace to drop, meaning reduction and iron melting are not continuous.
To address this, a method of injecting high-temperature hydrogen into the blast furnace has been considered. But due to the flammability of hydrogen, determining how and where to heat it to what degree has proven challenging.
Furthermore, the structure of blast furnaces is premised on coal usage. Taisuke Horimi, in charge of Green Transformation Development at Nippon Steel, commented on these challenges. "A 100% substitution of hydrogen for carbon is problematic. With hydrogen injection, unknown temperature changes occur alongside exothermic and endothermic reactions within the furnace," he reported.
50% Cut is the Goal
Nippon Steel is steadily working toward a 50% CO2 reduction in blast furnaces by effectively controlling these two challenges related to temperature using advanced technologies. The company will attempt to both increase the amount of hydrogen injected and optimize temperature control.
Steelworks consist mainly of two types of furnaces – blast furnaces and electric furnaces that melt scrap steel using electricity. Amid decarbonization efforts, there is a growing trend to use electric furnaces that emit less CO2 during production. However, according to Horimi, "the amount of scrap steel in circulation cannot meet the global demand for steel."
The company aims to commercialize hydrogen reduction technology for blast furnaces by 2040 to ensure a stable supply of the steel needed to support our society.
このページを 日本語 で読む