Digital Transformation: Creating Better Workplaces for Women in the Industrial Waste Industry
A leading company in industrial waste, Tsuneishi Kamtecs has implemented a digital transformation (DX), with women taking on increasingly prominent roles.
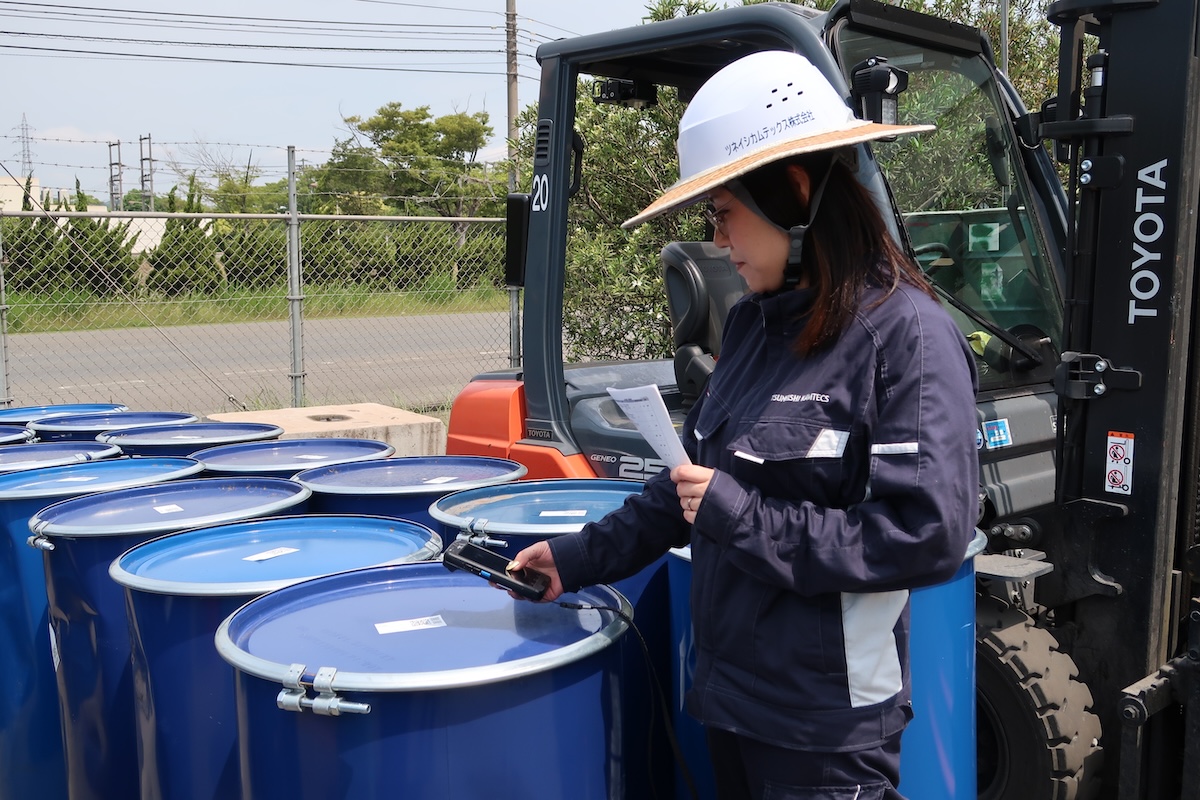
このページを 日本語 で読む
Women are making significant contributions in the industrial waste disposal industry, an area where women were often absent in the past. Japan 2 Earth spoke with Hiroko Tsujita of Tsuneishi Kamtecs about implementing the company's digital transformation (DX) strategy. Tsujita played a pivotal role in streamlining work processes to establish a more female-friendly workplace. By abolishing paper and establishing a waste information management system, Tsuneishi Kamtecs created a work environment more conducive to balancing work and family responsibilities.
Becoming a Regular Employee
What prompted you to join Tsuneishi Kamtecs?
I studied information processing for three years at a commercial high school in Okayama, but I only learned the basics of programming. After graduation, I worked as a sales assistant at a credit card company and insurance agency but ended up resigning from those positions. That's when the CEO of Tsuneishi Kamtecs at the time approached me. Rather than being drawn to the environmental or recycling aspects, I joined the company with the simple desire to become a regular full-time employee (laughs).
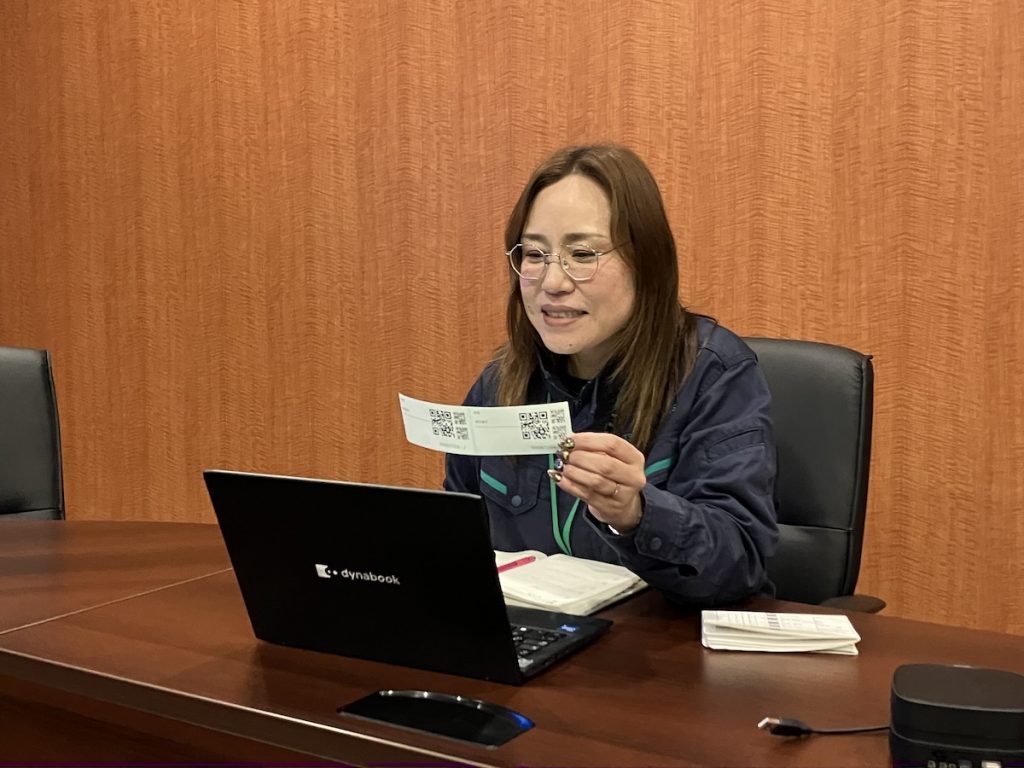
When I first joined, I worked as a sales clerk, inputting data on incoming waste into the system. We were using a general-purpose system to manage waste. Using it was cumbersome because the data was too heavy and the system frequently crashed.
You were put in charge of the system in November 2018. Did your background in information processing help?
While my background in information processing was recognized, it was knowledge from over ten years ago. So I had to start from scratch. At the time, we had introduced Salesforce, a globally recognized system, to manage our waste data. But we were using it much like a "box" to put our data in. Interdepartmental communication and approvals were still being done on paper with approval stamps. All the back and forth between computers and printers made it quite inefficient. Even though I was put in charge of the system, I had no idea where to start. So I began to consider the possibilities.
Paper and Rubber Bands
Tsujita started small and focused on streamlining office tasks. Significant improvements were made to the layout of the screen for registering waste disposal information. These enabled employees to easily view registration information for incoming waste and histories at a glance. The company was then able to go paperless. With these improvements, work processes were reduced to less than a third despite a doubling in the number of registrations for incoming waste. The total reduction in work time annually amounted to 900 hours.
Could you describe work tasks before your digital transformation strategy?
We see a lot of variety in the waste we receive from customers. This requires accurate and detailed management of information. The waste we bring in exceeds 500 drum cans on an average day, and there can be over 1,000 drums on busy days. Additionally, waste comes packaged in various ways, such as flexible container bags, pallets, dump trucks, and lorries. We had to register this information, make decisions, and obtain approvals in advance. Even when electronic data was sent via email, we had to convert each piece of data, including photos and documents related to the material into PDF files. We then printed these out and put them together. The volume of paper meant we couldn't staple them together and sometimes had to bundle them with rubber bands.
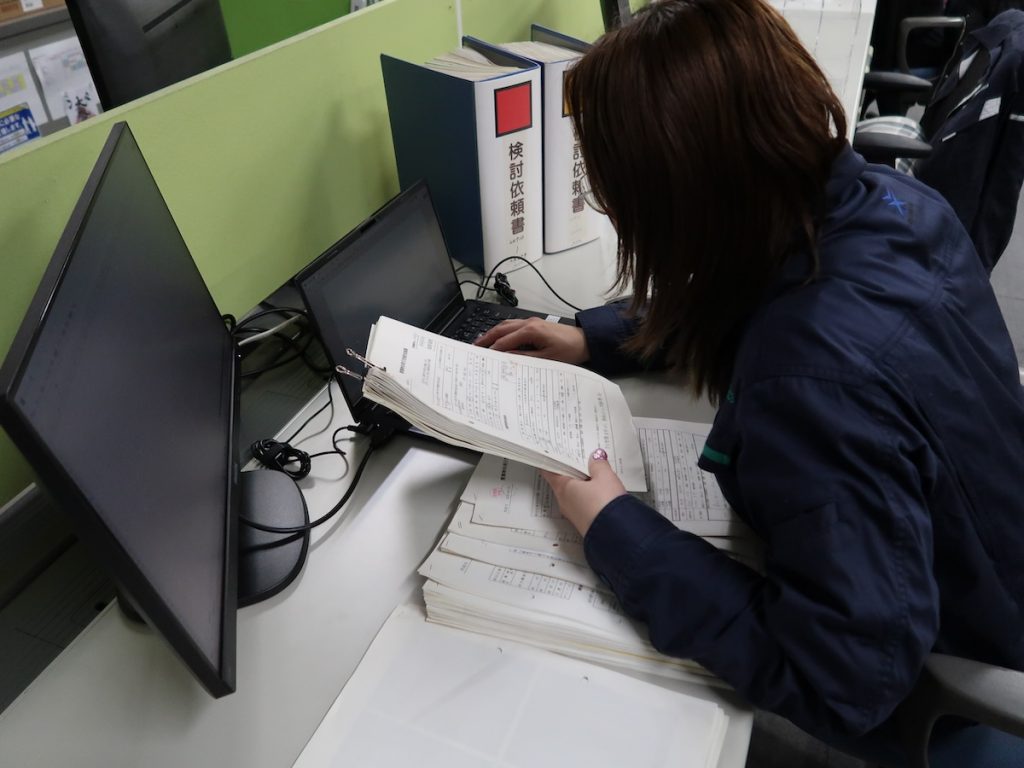
The documents were physically carried and placed into a box to await approval. Once they'd received a stamp, they were passed on to the next level for approval. We had to repeat this process for each approval. All comments related to decisions on whether the waste was acceptable for processing also had to be registered as data. The company's server couldn't be accessed remotely. So whenever we needed to check on something, we had to call the office and ask someone to check it for us.
How long did this process take?
Each step took between 5 to 10 minutes as we had to open Excel and confirm each detail. Approvals took one to two weeks to come back as the approvers would review one week's worth of paperwork at a time.
Launch of 'Special Project'
As part of the digital transformation strategy, Tsujita began to make improvements to the system based on her own experiences and the opinions of colleagues. The company achieved time savings in office work, but the system development itself was carried out by a separate company. This made it hard for Tsujita to take advantage of her status as a system administrator.
In June 2019, she was assigned to a "Special Project" aimed at addressing internal company issues. There she began to develop a system that could manage individual pieces of waste as a fully engaged system administrator.
It must have been quite a challenge to manage 1,000 drum cans a day?
Honestly, it was overwhelming. When we were developing the individual waste management system based on QR codes, I made multiple visits to waste transportation and processing sites to experiment and troubleshoot.

Particularly concerning was the risk QR code labels being applied incorrectly, leading to discrepancies between the information and the actual waste. To address this, we initially affix "empty" QR codes to incoming waste that don't contain any information. We then use a handy terminal to read the waste information, which is managed separately, and link it to the QR codes affixed to the waste.
We also made sure that individual waste information could be centrally managed in Salesforce.
QR Code Trials and Tribulations
The QR code labels themselves were the cause of much trial and error.
Did you struggle with selecting QR code labels?
Some waste is stored outdoors. So, we had to ensure that the labels wouldn't deteriorate due to UV rays. We plastered labels saying "test underway" here are there on various surfaces. We even tested water resistance by spraying water on them multiple times. Eventually, we opted for plastic labels and an adhesive commonly used for frozen foods. We also deliberated on the size of the labels. Making them larger would increase the cost of the labels themselves. It took several months to make a final decision. By then, I was seeing QR codes in my dreams! Selecting a device was another challenge. I made many site visits before we adopted anything. We also decided to put two identical labels on each item to protect against label damage or the label becoming hard to see when stacked.
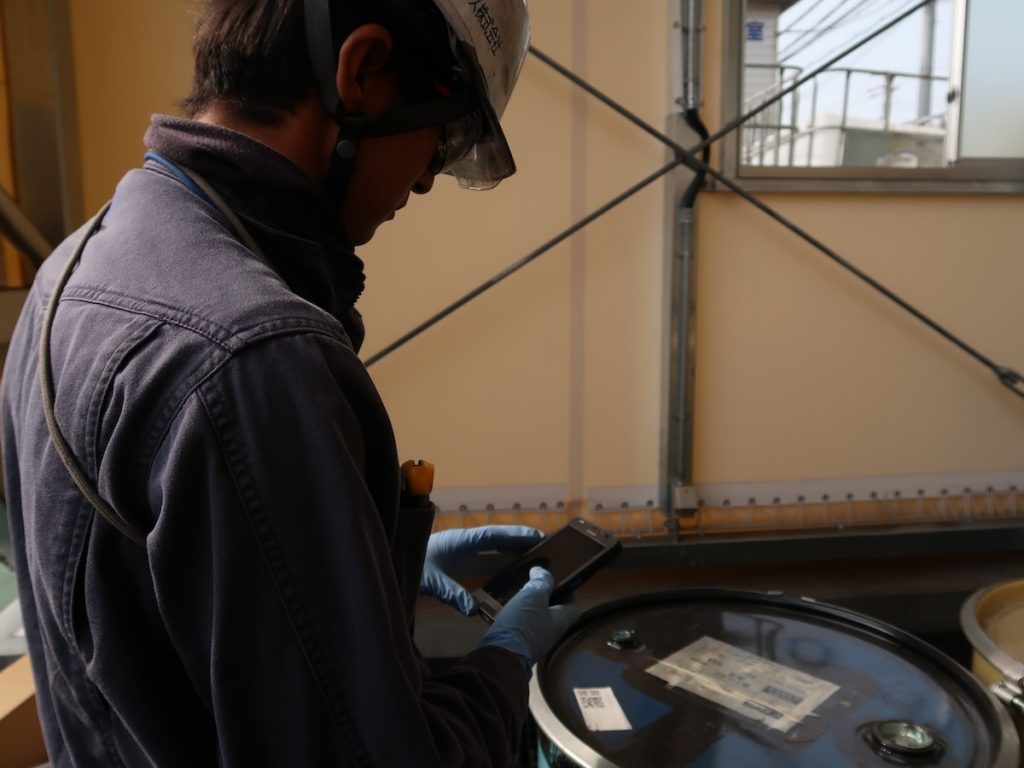
Were there significant benefits to individual waste management?
Now when we have any sort of trouble, like heating due to the mixing of foreign substances, we can instantly determine which item of waste is responsible. Previously, we had to rely on the intuition and experience of veteran employees. We'd ask them, "Could it have been that drum we received on such-and-such date?" Additionally, we can accurately manage inventory and predict the levels of pollutants such as hydrogen chloride and sulfur oxides in combustion gas generated during processing.
Digital of Waste Vehicle Entries
Even those initially hesitant about the digital transformation of our system gradually recognized the convenience of managing waste information using Salesforce. Tsujita's colleagues began bringing her suggestions. One such improvement concerned managing the entry of waste transport vehicles.
Were vehicle queues quite long?
We used to manually write out the order of entry of vehicles. When the queues got long, there could be over 30 trucks, some waiting for over three hours. In December 2021, we developed an app for scheduled entry data. We could then utilize handy terminals, the same ones used for QR codes. This allowed us to check in and direct waiting vehicles to their unloading locations from the handy terminal's screen. We also enabled drivers to receive entry instructions via text messages on their smartphones.
Simultaneously, we abolished paper approvals for estimates and the stamping of paper contracts, streamlining business processes related to sales.
'Mom, That's Amazing'
Tsujita reflects on the challenges of balancing work and family and work. She has realized that being a mother and a woman allowed her to address the needs of women like her in the company's digital transformation.
Do you think the perspective of women was incorporated into the digital transformation strategy?
Yes, I do. My son is now in college, but he was still in elementary school when I joined the company. The burden of administrative work at the time meant frequent overtime and he must have missed me. I used to prepare meals for the next day during dinner time. Although my husband supported me, he sometimes had business trips. It was extremely tough at times so much so that I'd rather not even think about it. So, I had a strong desire to streamline our operations and eliminate overtime to allow women to leave work on time. And not just their home lives, I want them to have free time to enjoy their lives. I was thinking much like a mother! Creating a system that could directly address these needs was very important to me.
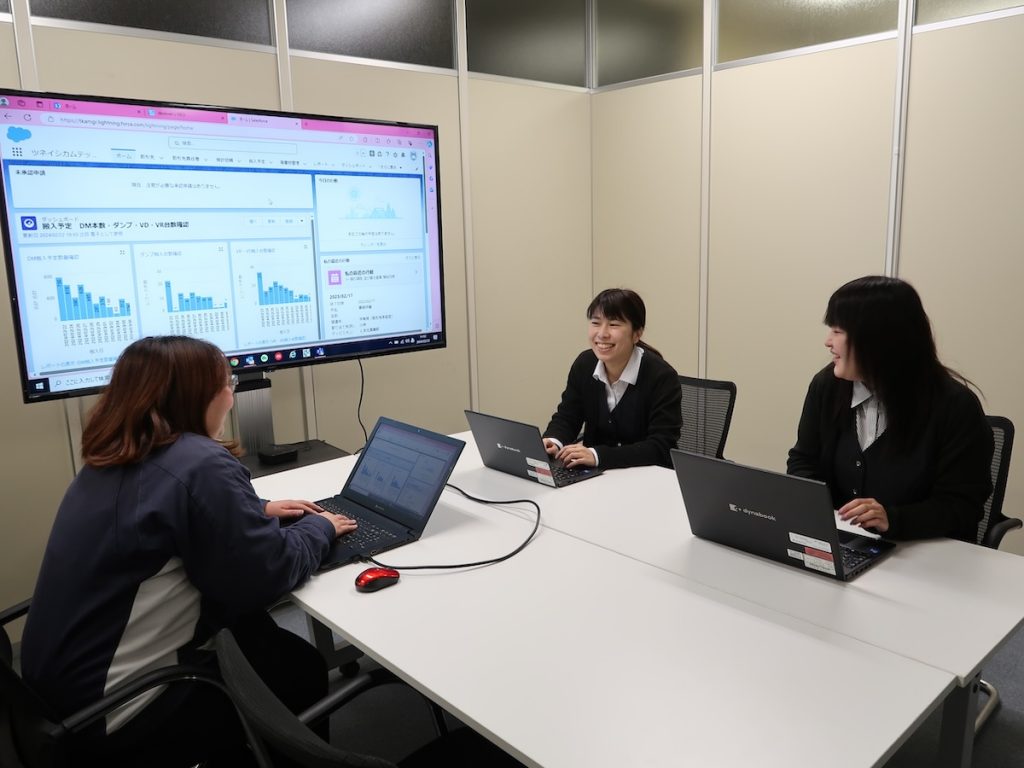
You participated in the finals of the Small and Medium-sized Enterprises Division of the SFUG CUP 2023, Salesforce Japan Use Case Contest. How was it?
Participating in the tournament allowed me to showcase the success of our efforts. Many things came together. While we didn't win the championship, my son was encouraging, saying "Mom, that's amazing." That's the best compliment I could have received.
Please tell me about your future goals.
I hope to leverage the experience and knowledge gained from our waste information management system to address other challenges in the industry. It has become more commonplace to see women driving large tank lorries, but the number of women in this industry is still quite small. I want to create an environment where women can not only easily enter this industry, but enjoy their work within it.
The Tsuneishi Kamtecs Corporation is a logo partner of Japan 2 Earth.
このページを 日本語 で読む